
Indoor Mill LiDAR Scanning
Introduction
Recently, our team was called upon to assist a mill in a critical infrastructure project. The mill is converting its existing fuel oil burners to natural gas burners—an upgrade that has far-reaching benefits in terms of operational efficiency, environmental impact, and long-term cost savings. Our role in this project was to perform highly detailed terrestrial LiDAR scanning of the mill’s buildings and equipment using a Leica RTC360 laser scanner, then process the data using Leica’s Cyclone REGISTER 360 software. The result was a precise 3D model that engineers and facility managers can rely on for design, planning, and execution of the burner conversion project.
In this blog post, we’ll delve into the why and how of the fuel conversion process, outline the technical details of the LiDAR scanning, and describe our post-processing approach. We’ll close with a few resources where you can learn more about this technology and its applications.
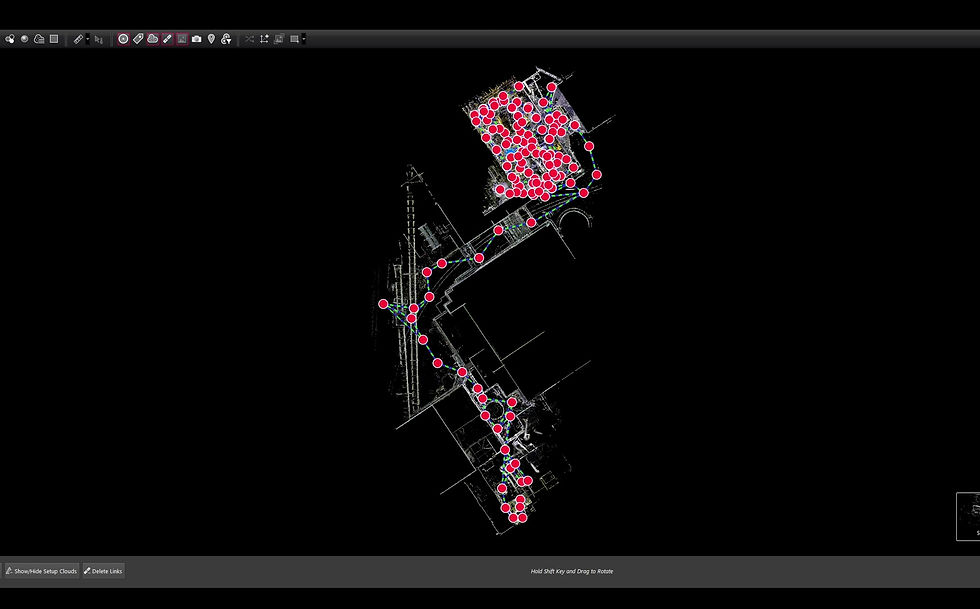
Fuel Oil to Natural Gas Conversion: Why It Matters
-
Reduced Emissions:
Converting from fuel oil to natural gas reduces greenhouse gas emissions, lowers particulate pollution, and helps facilities meet more stringent environmental regulations. In a paper mill context—where large volumes of steam are required—this makes a notable difference in the plant’s overall carbon footprint. -
Operational Savings:
Natural gas burners often deliver lower operating costs compared to fuel oil, due to higher energy efficiency and stable pricing. Over time, these savings can be reinvested into other facility upgrades or research and development. -
Improved Reliability:
Natural gas supply lines are typically more stable than fuel oil deliveries, reducing the risk of fuel shortages. Fewer on-site deliveries are also beneficial in terms of logistics and safety. -
Reduced Maintenance:
The cleaner combustion process of natural gas translates into fewer deposits and less equipment wear, which can reduce maintenance costs and downtime.

Terrestrial LiDAR Scanning with the Leica RTC360
-
Why Terrestrial LiDAR?
Terrestrial LiDAR (Light Detection and Ranging) scanning offers incredibly detailed 3D data of existing conditions.
By capturing millions of measurement points in minutes, this technology provides a precise digital replica of indoor and outdoor spaces. When dealing with complex industrial layouts—such as a paper mill—accurate as-built documentation is crucial for planning retrofits like burner replacements.
-
Leica RTC360 System Overview:
-
Speed and Accuracy: The RTC360 can capture up to 2 million points per second, reducing the time needed on-site. It also maintains a high range of accuracy, typically within millimeters, depending on the environment and setup.
-
Automatic Registration On-The-Fly: The RTC360 features an advanced Inertial Measurement Unit (IMU) and visual-inertial system that helps align consecutive scans in real time. This allows for faster field workflows by minimizing the amount of manual target alignment required afterward.
-
Compact and Portable: Due to its relatively small form factor, the RTC360 is easy to move and set up in multiple locations, even in tight, industrial environments.
-
-
Scan Planning and Field Execution:
-
Strategic Scanner Placement: Inside the mill, we needed to ensure comprehensive coverage of boilers, burner assemblies, piping, and walkways. Scanner positions were planned to avoid major obstructions while still capturing the necessary reference points.
-
Data Capture: In each position, the RTC360 performed a full 360-degree scan in a matter of seconds. For challenging areas, multiple overlapping scans were collected to make sure no critical features were missed.
-
Safety Considerations: Paper mills have unique hazards such as high heat, wet floors, and busy traffic from maintenance personnel. We coordinated closely with ND Paper staff to ensure each scanning position was set up safely and without disrupting their operations.
-

Post-Processing with Leica Cyclone REGISTER 360
-
Data Import and Automatic Alignment:
After fieldwork, the raw scans were imported into Leica Cyclone REGISTER 360. The software uses the RTC360’s pre-alignment (thanks to its IMU and cameras) to automatically register most of the scans in the correct relative positions. This significantly cuts down on the time needed for manual point-cloud alignment.
-
Cleaning and Noise Reduction:
Industrial environments can introduce noise in the form of dust, steam, or reflective surfaces. Cyclone REGISTER 360 includes robust tools to remove erroneous points. This step ensures a cleaner dataset and more accurate 3D model for subsequent work.
-
Cloud-to-Cloud and Target Registration:
In areas with tight tolerances, we performed a detailed cloud-to-cloud registration and used checkerboard or spherical targets for additional alignment accuracy. This further refines the entire point cloud, especially around critical mechanical features where precision is paramount.
-
Visualization and QA/QC:
The software’s intuitive interface allowed us to visualize each scan station, checking for holes or misalignments in the point cloud. Once everything was verified, Cyclone REGISTER 360 generated a unified point cloud model of the mill’s interior spaces—ready for use in CAD, BIM, or specialized piping design software.
-
Deliverables:
-
Unified Point Cloud: A single, registered dataset that engineers can import into 3D modeling environments to plan piping layouts, burner placements, and structural modifications.
-
Orthographic Views and Cross-Sections: 2D slices and detailed orthophotos extracted from the 3D data for direct measurement and design references.
-
Comprehensive Reporting: Cyclone REGISTER 360 can generate reports that document the registration process, residual errors, and final alignment accuracy, ensuring the integrity of the dataset for any subsequent design or construction work.
-
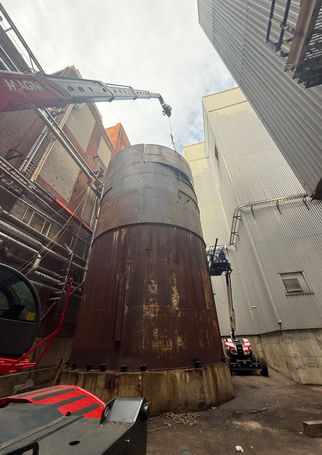
The End Result and Future Implications
By merging the high-fidelity data from the Leica RTC360 with the powerful registration features of Cyclone REGISTER 360, the mill's team now has a highly accurate 3D model of its buildings’ interior systems. This digital model is instrumental in:
-
Design and Engineering: Accurately planning and routing new gas lines and burner equipment.
-
Safety and Efficiency: Minimizing the risk of on-site measurements or guesswork during the transition.
-
Future Upgrades: Serving as a reliable baseline for any upcoming modifications or expansions within the facility.
The shift to natural gas burners and the utilization of LiDAR scanning technology epitomize how modern industry can balance productivity with sustainability. As the mill moves forward with the conversion, they’re paving the way for reduced emissions, lower operational costs, and a future-ready plant layout.
References and Further Reading
-
Leica Geosystems – RTC360
Official product page for the Leica RTC360, detailing technical specifications and use cases. -
Leica Cyclone REGISTER 360
Learn more about the software’s capabilities for LiDAR data registration and project management. -
Natural Gas Conversion Benefits – U.S. Department of Energy
General information about cleaner combustion, regulatory compliance, and cost benefits.
Thank you for reading! If you have any questions about terrestrial LiDAR scanning, facility as-built documentation, or how modern surveying technologies can support industrial upgrades, feel free to reach out to our team. We’re always here to help you capture and transform your spaces more efficiently, accurately, and sustainably.
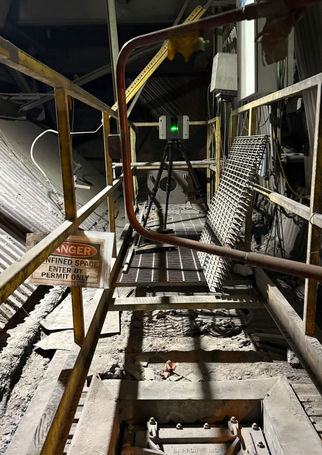